AXIC BenchMark 800® ETCH and DEPOSITION
A cost-effective plasma processing system for Reactive Ion Etching and/or Plasma Enhanced Chemical Vapor Deposition
The BenchMark 800 Plasma Processing System from Axic, Inc. defines a new concept in RIE and PECVD plasma processing Systems. The system is based on a modular design starting with a universal chamber and cabinet unit with Planar, RIE and PECVD electrode modules available for easy installation into the chamber unit. We’re confident you’ll find the ease of use, variety of plasma processes, serviceability and attractive pricing of the BenchMark 800-II® unsurpassed by any other plasma product on the market.
SYSTEM DESCRIPTION
In the research and development of plasma processing, there has always been a great need for a highly versatile and reliable tool. With ever changing requirements in plasma research, the system selected must offer the widest range of process parameters, a high degree of repeatability for process verification, and must he easily modified for new process requirements.We believe that the BenchMark 800® series of dry process systems satisfies these very demanding requirements.The BenchMark 800® is a plasma tool used in research, process development or low volume production for precise etching and deposition on substrates up to eight inches in diameter. The system can be operated in either a batch or single slice mode.In designing the BenchMark 800®, the prime directive was to create a system that incorporates the quality, reliability, repeatability and process control capabilities of dedicated production-oriented systems, while drastically reducing cost, maintenance and floor space requirements.The BenchMark 800-II®’s unique cabinet and electrode design allows for easy installation in a laminar flow module or clean room. Selection of proven, quality components, modular sub-assemblies, versatile chamber and electrode design, compact size, automation and field-proven process recipes make the BenchMark 800® from Axic, Inc. the plasma engineer’s “system of choice.”
Features
- Single-piece chamber construction
- In-situ electrode spacing (PECVD version)
- Replaceable gas showerhead
- Proven process recipes
- Field-proven components
- Endpoint detection (option)
- Multiple electrode configurations
- Auto RF matching
- Downstream pressure control (option)
- Computer control with Windows programming
- Multiple pumping options: mechanical, mechanical/blower, turbo
- Single chamber and dual chamber versions
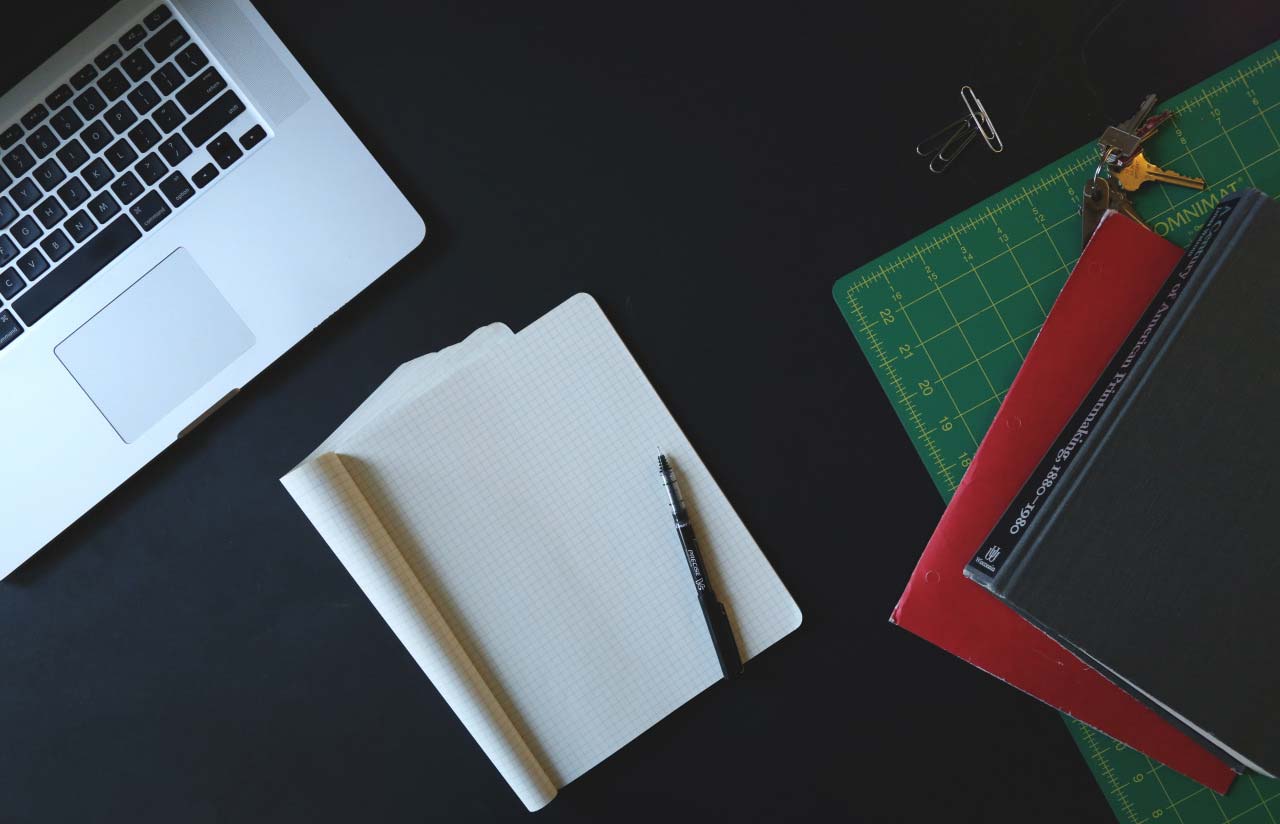
Applications
With its generous seTection of processing modules, the BenchMark 800® satisfies a broad range of plasma processing conditions, from sophisticated submicron RIE etching to deposition of high quality PECVD films. A list of typical processes is shown below.Working closely with our large customer base, we have developed field-proven process recipes, guaranteeing that your system will be up and running from the day you install it. Only the highest quality sub-components are used in manufacture, ensuring that your BenchMark 800-II system will provide the highest possible uptime, reliability, repeatability and serviceability.
- Failure analysis applications
- Material modification
- Adhesion promotion Plasma descum
- Surface treatment
- Anisotropic and isotropic etching
- Metal etching
- Si02, Si3N4 and SiOxNy deposition
- III-V etching applications
- Trench etching
- Passivation etching
- Polyimide etching
- Submicron etching
Specifications
The popularity of the BenchMark 800-II® is due primarily to its attractive cost of ownership and a highly versatile design, providing features and process benefits not found on most systems. These include a small footprint for laminar flow installations and multiple electrode configurations. Substrates up to eight inches in diameter can be processed.
Basic system
Basic components in the BenchMark 800® system include a Windows-based PC controller with recipe storage, two channels of mass flow control with expansion of up to six channels, temperature compensated capacitance manometer for measurement of process vacuum, 1OOmm vacuum plumbing for maximum process gas conductance, KF or ISO, fittings for ease of service, plus many other processing and service features. Gas lines are stainless steel with VCR connections.
Process Chamber
The BenchMark 800®s aluminum process chamber is constructed from a unique “single-piece” design. RIE, PECVD and Parallel Plate systems use the same chamber design. The chamber’s upper portion contains the top electrode and is available with in-situ variable electrode spacing. The lower portion contains the substrate electrode, the vacuum pumping port and all necessary valves and vacuum monitoring equipment. An automatic hoist raises the upper portion of the chamber for easy access to the lower electrode.

Electrodes
The RIE series of electrodes are specifically designed for maximum performance in the lower vacuum ranges. The stainless steel upper electrode contains the “showerhead” gas delivery system. The stainless steel bottom electrode is temperature controlled via an optional recirculating liquid bath. The RIE cathode is supplied with a dark space shield, confining the plasma between the two electrodes. The PECVD electrodes are of similar design. However, the aluminum lower substrate electrode is capable of being heated to 400°C, while the upper electrode (powered) is water cooled. The aluminum electrode has a gas induction port for rapid cool down after completion of deposition. For PFCVD applications the upper electrode spacing can be continuously varied between 1″ and 3.5″.
Plasma sources
A broad range of power and plasma frequences is available. All power sources are solid state and air cooled wherever possible. Available power ranges from 300 to 1250 Watts and RF frequencies from 40 KHz to 2.45 GHz, with 13.56 MHz/6OO watts being standard. Aut o or manual matching networks are supplied where necessary.
Process pumping
The system is supphed either with a mechanical pump, mechanical pump and turbomolecular pump, or mechanical pump with Roots Blower, depending on process requirements. Various sizes of these pumps are available based on the required vacuum processing levels.
Controller
A Pentium computer is employed for complete system control. This includes a hard drive, 1.44MB floppy disk drive’e, 8MB DRAM and a clock-calendar. Complete Windows software using multiple display windows for equipment control, datalogging, recipe setup and storage, and system interlocking is provided.
Options
To further increase its capabilities, the BenchMark 8OO-II® offers a broad selection of available processing options, including endpoint detection, water chillers, oil filtration and purging systems, downstream pressure control and hard-anodized chamber. Exhaust gas abatement systems can also be supplied.The dual chamber system can be configured in any combination of RIE and PECVD. While a RIE/PECVD combination is the more obvious for versatility, a PECVD/PECVD combination is useful in avoiding cross-contamination for different deposition processes.
Dimensions
Single Chamber | Dual Chamber | |
Width: | 36″ | 41″ |
Depth: | 32″ | 45″ |
Cabinet Height: | 36″ | 36″ |
Total Height: | 51″ | 51″ |
Weight
150-250 lbs. (depending on options).
Utilities
System: | 110 V, 60Hz, 15 Amps |
220 V, 50 Hz, 7 Amps (optional) | |
Pump: | 110 V, 60 Hz, 10 Amps (mechanical only) |
220 V, 50 Hz, 5 Amps | |
Water: | For electrode cooling (70°F ± 5°F) |
Air: | For valve operation (80 psi) |
N2: | For chamber vent (15-20 psi) |
Gas: | Process gasses, VCR fittings. |